RANDOM POSTs
-
Lumotive Light Control Metasurface – This Tiny Chip Replaces Bulky Optics & Mechanical Mirrors
Read more: Lumotive Light Control Metasurface – This Tiny Chip Replaces Bulky Optics & Mechanical MirrorsProgrammable Optics for LiDAR and 3D Sensing: How Lumotive’s LCM is Changing the Game
For decades, LiDAR and 3D sensing systems have relied on mechanical mirrors and bulky optics to direct light and measure distance. But at CES 2025, Lumotive unveiled a breakthrough—a semiconductor-based programmable optic that removes the need for moving parts altogether.
The Problem with Traditional LiDAR and Optical Systems
LiDAR and 3D sensing systems work by sending out light and measuring when it returns, creating a precise depth map of the environment. However, traditional systems have relied on physically moving mirrors and lenses, which introduce several limitations:
- Size and weight – Bulky components make integration difficult.
- Complexity – Mechanical parts are prone to failure and expensive to produce.
- Speed limitations – Physical movement slows down scanning and responsiveness.
To bring high-resolution depth sensing to wearables, smart devices, and autonomous systems, a new approach is needed.
Enter the Light Control Metasurface (LCM)
Lumotive’s Light Control Metasurface (LCM) replaces mechanical mirrors with a semiconductor-based optical chip. This allows LiDAR and 3D sensing systems to steer light electronically, just like a processor manages data. The advantages are game-changing:
- No moving parts – Increased durability and reliability
- Ultra-compact form factor – Fits into small devices and wearables
- Real-time reconfigurability – Optics can adapt instantly to changing environments
- Energy-efficient scanning – Focuses on relevant areas, saving power
How Does it Work?
LCM technology works by controlling how light is directed using programmable metasurfaces. Unlike traditional optics that require physical movement, Lumotive’s approach enables light to be redirected with software-controlled precision.
This means:
- No mechanical delays – Everything happens at electronic speeds.
- AI-enhanced tracking – The sensor can focus only on relevant objects.
- Scalability – The same technology can be adapted for industrial, automotive, AR/VR, and smart city applications.
Live Demo: Real-Time 3D Sensing
At CES 2025, Lumotive showcased how their LCM-enabled sensor can scan a room in real time, creating an instant 3D point cloud. Unlike traditional LiDAR, which has a fixed scan pattern, this system can dynamically adjust to track people, objects, and even gestures on the fly.
This is a huge leap forward for AI-powered perception systems, allowing cameras and sensors to interpret their environment more intelligently than ever before.
Who Needs This Technology?
Lumotive’s programmable optics have the potential to disrupt multiple industries, including:
- Automotive – Advanced LiDAR for autonomous vehicles
- Industrial automation – Precision 3D scanning for robotics and smart factories
- Smart cities – Real-time monitoring of public spaces
- AR/VR/XR – Depth-aware tracking for immersive experiences
The Future of 3D Sensing Starts Here
Lumotive’s Light Control Metasurface represents a fundamental shift in how we think about optics and 3D sensing. By bringing programmability to light steering, it opens up new possibilities for faster, smarter, and more efficient depth-sensing technologies.
With traditional LiDAR now facing a serious challenge, the question is: Who will be the first to integrate programmable optics into their designs?
-
Deep Compositing in Nuke – a walkthrough
Read more: Deep Compositing in Nuke – a walkthroughDepth Map: A depth map is a representation of the distance or depth information for each pixel in a scene. It is typically a two-dimensional array where each pixel contains a value that represents the distance from the camera to the corresponding point in the scene. The depth values are usually represented in metric units, such as meters. A depth map provides a continuous representation of the scene’s depth information.
For example, in Arnold this is achieved through a Z AOV, this collects depth of the shading points as seen from the camera.
(more…)
https://help.autodesk.com/view/ARNOL/ENU/?guid=arnold_user_guide_ac_output_aovs_ac_aovs_html
https://help.autodesk.com/view/ARNOL/ENU/?guid=arnold_for_3ds_max_ax_aov_tutorials_ax_zdepth_aov_html
COLLECTIONS
| Featured AI
| Design And Composition
| Explore posts
POPULAR SEARCHES
unreal | pipeline | virtual production | free | learn | photoshop | 360 | macro | google | nvidia | resolution | open source | hdri | real-time | photography basics | nuke
FEATURED POSTS
-
Google – Artificial Intelligence free courses
-
Sensitivity of human eye
-
What Is The Resolution and view coverage Of The human Eye. And what distance is TV at best?
-
Alejandro Villabón and Rafał Kaniewski – Recover Highlights With 8-Bit to High Dynamic Range Half Float Copycat – Nuke
-
Generative AI Glossary / AI Dictionary / AI Terminology
-
59 AI Filmmaking Tools For Your Workflow
-
Godot Cheat Sheets
-
Photography basics: Production Rendering Resolution Charts
Social Links
DISCLAIMER – Links and images on this website may be protected by the respective owners’ copyright. All data submitted by users through this site shall be treated as freely available to share.
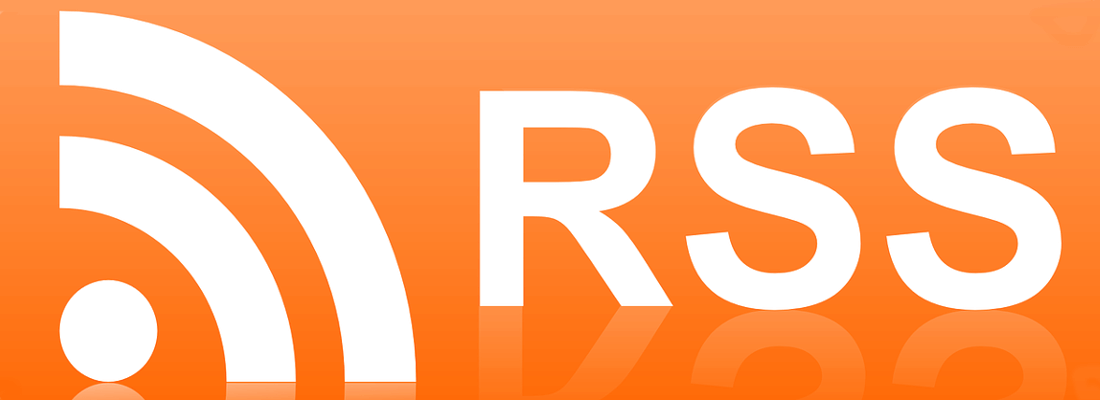